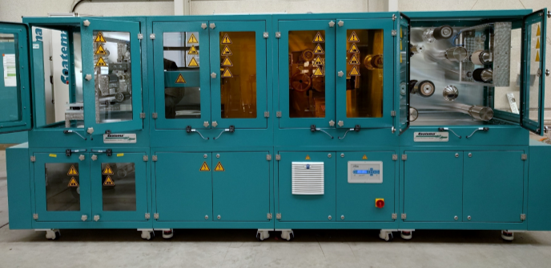
Roll-to-Roll Manufacturing
A key activity in our research group is the development of scalable methods to process nanomaterials into well-defined structures. With the discovery of new nanomaterial structuring, a variety of new exciting material properties have emerged, which rely on a well controlled organisation of the nanoparticles. Directed self-assembly has proven to be a highly promising route to control the organisation of nanomaterials, but to date, deterministically controlling the nanoscale material organisation remains challenging, in particular when using scalable manufacturing processes that allow for square meter scale processing. In our group we apply self-assembly and other advanced self-organisation processes to control material morphology on a pilot scale Roll-to-Roll coater. We have used roll-to-roll coater for fabricate thin film CNT heaters, photonic materials and Li-Ion battery electrodes.
Photonic Materials
Hydroxypropyl-cellulose (HPC), a derivative of naturally abundant cellulose, can self-assemble into helical nanostructures that lead to striking colouration from Bragg reflections. The helical periodicity is very sensitive to pressure, rendering HPC a responsive photonic material. Recent advances in elucidating these HPC mechano-chromic properties have so-far delivered few real-world applications, which require both up-scaling fabrication and digital translation of their colour changes. Here we present roll-to-roll manufactured metre-scale HPC laminates using continuous coating and encapsulation. This process is depicted in the image below and is carried out in collaboration with the groups of Prof. Silvia Vignolini and Prof Jeremy Baumberg at the University of Cambridge.
We also quantify the pressure response of the encapsulated HPC films using optical analyses of the pressure-induced hue change as perceived by the human eye and digital imaging. Finally, we show the ability to capture real-time pressure distributions and temporal evolution of a human foot-print on our HPC laminates. This is the first demonstration of a large area and cost-effective method for fabricating HPC stimuli-responsive photonic films, which can generate pressure maps that can be read out with standard cameras. As an example, the pressure under distribution under a foot was analysed using our mechanochromic HPC films as depicted below. More information can be found here.
Li-Ion Battery Electrodes
To date, roll-to-roll coating is the only commercially viable process to manufacture Li-Ion batteries. In our research group we therefore study methods to integrate advanced Li-Ion battery materials on Roll-to-Roll processes. An first important step towards this is the development of continuous manufacturing processes allowing to fabricate sufficient amounts of material. One process we are investigating to achieve are continuous CVD processes which we are developing in collaboration with Dr Adam Boies at the University of Cambridge. More information on this process can be found here.
We developed a scalable process to fabricate SiFeCNT secondary particles for LI-Ion battery anodes that can be used either by themselves or blended with graphite. These particles are fabricated by spray-drying primary Si particles (∼50 nm diameter) into spherical secondary particles (∼3 μm diameter) to improve their packing density and reduce the amount of binder needed in the electrode formulation. Next, CNTs are grown directly from the surface of the Si particles using a continuous CVD process, and we found that the nanotubes are formed both inside and outside of the secondary particles leading to better electron transport. In addition, the CVD-grown CNTs are strongly anchored on the secondary particles, and as a result, phase segregation challenges during mixing and coating are mitigated and the electric network is maintained during cycling.
Pure SiFeCNT electrodes show a capacity of over 1150 mAh/g after 300 cycles at 1A/g and retain over 43% of their capacity at a rate of 5C. In addition, we present blend electrodes where SiFeCNT is mixed with graphite to obtain a 550 mAh/g anode. These were calendared to obtain industrially relevant loading levels (>6.5 mg/cm2 and >1.5 g/cm3) and show a CE of 99.5 from second cycle and capacity retention of 96.6% after 50th cycle. Finally, we demonstrate the scalability of our process by a coating a 35 m long electrode on a roll-to-roll tool. The process is depicted below, and more information can be found here.